Commentary | Peer reviewed |
Cite as: Cochrane RA, Dritz SS, Woodworth JC, et al. Feed mill biosecurity plans: A systematic approach to prevent biological pathogens in swine feed. J Swine Health Prod. 2016;24(3):154–164.
Also available as a PDF.
SummaryDevelopment of a feed mill biosecurity plan can minimize risk of introduction of biologic hazards and limit potential economic losses from animal or human pathogens such as Salmonella and porcine epidemic diarrhea virus. A biosecurity plan should be detailed and contain hazard controls at each step of the manufacturing process. Biologic hazards can cause illness or injury in humans or animals. These hazards can be introduced through a number of means, including ingredients, manufacturing equipment, or people, so controls must aim to prevent or reduce their prevalence. The Food Safety Modernization Act requires most feed mills to identify and control hazards. A biosecurity plan can serve as an effective prerequisite program to reduce the likelihood of a biological hazard occurrence by identifying ingredient specifications, sampling methods, analytical procedures, receiving guidelines, equipment cleanout, production parameters, load-out, and sanitation procedures. The objective of this review is to describe biological hazards that may be present in swine feed, locations of their potential entry, and suggested practices for a successful biosecurity plan for feed mills manufacturing swine feed. | ResumenEl desarrollo de un plan de bioseguridad para la planta de alimento puede minimizar el riesgo de introducción de peligros biológicos y limitar pérdidas económicas potenciales de patógenos humanos o animales tales como la Salmonella y el virus de la diarrea epidémica porcina. Un plan de bioseguridad debe ser muy detallado y contener los controles de riesgos para cada paso del proceso de manufactura. Los riesgos biológicos pueden causar enfermedad o lesión en humanos o animales. Estos riesgos pueden introducirse a través de varios vías, incluyendo los ingredientes, equipo de manufactura, o gente, por lo que los controles deben buscar prevenir o reducir su prevalencia. La Ley de Modernización de Seguridad de Alimento requiere que la mayoría de las plantas de alimento identifiquen y controlen los riesgos. Un plan de bioseguridad puede servir como un programa de prerrequisito efectivo para reducir la posibilidad de que ocurra un riesgo biológico al identificar las especificaciones de los ingredientes, métodos de muestreo, procedimientos analíticos, normas de recepción, limpieza de equipo, parámetros de producción, descarga, y procedimientos de saneamiento. El objetivo de esta revisión es describir los riesgos biológicos que pueden presentarse en el alimento porcino, localización de su potencial entrada, y prácticas sugeridas para un plan de bioseguridad exitoso para las plantas de alimento que manufacturan alimento porcino. | ResuméLa mise au point d’un plan de biosécurité à la meunerie peut minimiser le risque d’introduction de risques biologiques et minimiser le potentiel de pertes économiques dues à des agents pathogènes animal ou humain tel que Salmonella et le virus de la diarrhée épidémique porcine. Un plan de biosécurité devrait être détaillé et posséder des points de maitrise des risques à chaque étape du processus de fabrication. Les risques biologiques peuvent causer des maladies ou blessures chez les humains ou les animaux. Comme ces risques peuvent être introduits de plusieurs façons, incluant les ingrédients, l’équipement manufacturier, ou les personnes, les mesures de maitrise doivent viser à prévenir ou réduire leur prévalence. La règlementation du Food Safety Modernization Act exige que la majorité des meuneries identifie et maitrise les risques. Un plan de biosécurité peut agir comme un programme prérequis efficace pour réduire la possibilité d’apparition d’un risque biologique en identifiant les spécifications des ingrédients, les méthodes d’échantillonnage, les procédures analytiques, les directives pour la réception, le nettoyage de l’équipement, les paramètres de production, le chargement, et les procédures de désinfection. L’objectif de la présente revue est de décrire les risques biologiques qui peuvent être présents dans une meunerie d’alimentation porcine, la localisation de leur entrée possible, et suggérer des pratiques pour un plan de biosécurité réussi pour une meunerie produisant de la nourriture pour les porcs. |
Keywords: swine, feed, biosecurity, hazard analysis, pathogen control
Search the AASV web site
for pages with similar keywords.
Received: October 26, 2015
Accepted: December 2, 2015
Feed mill biosecurity is important to the feed and animal-agriculture industries as a way to control the spread of feedborne diseases and other hazards. Recent outbreaks of porcine epidemic diarrhea virus (PEDV) in the swine industry have increased awareness that biological hazards may be of concern in animal food manufacturing, which has stressed the importance of extending biosecurity procedures to the feed mill. According to the Food and Drug Administration (FDA), a hazard is “any biological, chemical (including radiological), or physical agent that has the potential to cause illness or injury in humans or animals.”1 Of course, implementing a biosecurity plan to mitigate biological hazards in a feed mill is challenging because of differences in facility design, manufacturing operations, and significant risk factors among feed mills.2 Regardless of those differences, a trained individual should first identify the potential hazards for the feed mill, evaluate their risks, and devise control measures to prevent or reduce their presence or severity. For hazards that are biological in nature, it is also important to consider methods to prevent cross-contamination throughout manufacturing. If at any point a biological hazard does enter the feed mill, feed recall and facility decontamination should be considered.
Most hazard analysis systems, including those required by the Food Safety Modernization Act (FSMA), allow facilities to consider prerequisite programs, such as a biosecurity plan, in their assessment of hazard probability. A properly designed and implemented feed-mill biosecurity plan minimizes the risk of biological pathogens in animal feed, which protects herd health, minimizes economic losses, and ultimately helps ensure farm-to-fork food safety.3 The objective of this review is to identify and evaluate potential biological hazards that may be present in swine feed, locations of potential entry of these hazards, and suggested practices for a feed mill biosecurity plan.
Hazards analysis
Identify ingredients and process steps
The first step of hazard analysis is to identify ingredients and process steps, which is usually most easily accomplished by creating a block flow diagram to visualize the major manufacturing processes within the feed mill (Figure 1). This diagram, which will vary by feed mill, allows one to easily identify the major processing steps that should be considered in a biosecurity plan for both points of potential hazard entry and control. Common categories in the diagram include receiving, processing, storage, packaging, loading, and delivery.3 A more complex flow with conveying systems can help to identify areas of higher risk for cross-contamination, but may also overcomplicate the process. The key is to accurately identify and list all ingredients and major steps in feed manufacturing.
Figure 1: Block flow diagram of a feed manufacturing process. Creating a flow diagram of a facility is an easy way to visualize which processes must be considered in the biosecurity plan. A more complex flow that includes conveying equipment may help isolate locations where cross-contamination is at higher risk to occur.

Hazard identification
Once the ingredients and process steps are identified, potential hazards associated with each should be determined. The comprehensiveness of this list can vary, but hazard identification is generally a brainstorming of all potential hazards that are known or reasonably foreseeable in the type of animal feed manufactured. That list of potential hazards is then evaluated for severity and probability to determine those that require control. According to FSMA, there are specific criteria that must be considered during hazard identification. These include the formulation, condition, function, and design of the facility and equipment, ingredients, transportation, processing procedures, packaging and labeling activities, storage and distribution, intended or reasonably foreseeable use of the feed, sanitation, and other relevant factors, as necessary.1 Resources are available to help individuals during this process, including scientific literature, FDA recalls,4 and FDA or other regulatory guidance.
Scientific literature demonstrating significant biological hazards in swine feed was limited prior to the introduction of PEDV to the United States in 2013. The virus causes diarrhea and vomiting in pigs of all life stages, but is most severe in suckling pigs, with mortality reaching close to 100% for 3 to 5 weeks and generating significant economic losses in North America.5 This coronavirus has also been found in Europe and Southeast Asia.6,7 Porcine epidemic diarrhea virus is primarily transmitted by the fecal-oral route.8-12 While pig-to-pig transmission is by far the most likely method of transmission, epidemiological evidence suggests that transport vehicles, fomites, feed, and aerosols may be involved in viral transmission due to cross-contamination with fecal material.9-11 Controlled research has confirmed that PEDV contamination in complete swine feed and ingredients can result in PEDV transmission.8-10
While PEDV was the first substantial biological hazard of concern in swine feed, other potential biological hazards exist. For example, mammalian orthoreovirus has recently been shown to be present in blood meal and result in infectivity.13 The most prevalent biological hazard in all animal feeds is undoubtedly Salmonella. Surveillance data from FDA cites that the contamination rate of Salmonella in all categories of animal feed and ingredients surveyed from 2002 to 2006 was 30.9%, but it dropped to 19.4% from 2007 to 2009.14 Contamination rate in complete feeds was much lower; it was 9.4% from 2002 to 2006 and 5.6% from 2007 to 2009.14
Outside of scientific literature, other resources, such as those from the FDA and other regulatory bodies, may be helpful during hazard identification. The FDA maintains a database of recalls and withdrawals, as well as the Reportable Food Registry, which documents facilities that report when there is a “reasonable probability that the use of, or exposure to, an article of food will cause serious adverse health consequences or death to humans or animals.”4 These lists may be helpful to help individuals conducting the hazard identification to understand hazards previously associated with the type of animal feed being manufactured. The FDA is actively developing guidance on hazards associated with different types of animal feed, but that has not been published at the time of this publication. Previously, the FDA has released a “Draft list of potentially hazardous contaminants in animal feed and feed ingredients” in 2006.15 While not comprehensive in nature, this list is a good resource for the hazard identification process, as it categorizes hazards into those that are physical, chemical, and biological in nature. The biological hazards are grouped into two categories: transmissible spongiform encephalopathies, including bovine spongiform encephalopathy and chronic wasting disease, and biological contaminants, including Bacillus species, Clostridium species, Escherichia coli, Mycobacterium species, Pseudomonas species, Salmonella enterica serovars, and Staphylococcus species.15 This list was established prior to the introduction of PEDV to the United States, and thus this potential hazard was not included on the list. Furthermore, many potential hazards included on the list are not known or reasonably foreseeable in swine feed. This emphasizes that multiple resources may be necessary for thorough hazard identification.
Hazard evaluation
The second step of hazard analysis is to evaluate the hazard’s severity and probability of occurrence within a single facility. As is the case with hazard identification, the determination of the severity and probability of each hazard is different for each facility because of multiple variables that change from one feed mill to another. The combination of severity and probability is used to set a threshold likely to require control.
The severity determination according to FSMA must assess the severity of illness or injury if the hazard were to occur.1 This severity assessment is flexible, but hazards that cause short-term injury or illness in a single animal would likely have a lower severity assessment than those that have the potential to cause widespread mortality. For example, the presence of metal in swine feed would likely have a lower severity than PEDV, because a metal bolt from a piece of manufacturing equipment is not likely consumed by an animal. If it is, the hazard is limited to a single animal and does not impact overall herd health. The presence of PEDV in swine feed would typically be evaluated as having greater severity than metal because of the likelihood for multiple deaths. Outside of the severity of the illness or injury and the potential number of animals affected, other factors can be considered in the overall severity assessment of the hazard. Depending on the facility, these may include the value of the animal to the production system or a hazard’s potential impact on human health.
In addition to evaluating the severity of a hazard, the individual conducting hazard analysis should also consider its probability of occurrence. This step is also required by FSMA, where individuals must “assess the probability that the hazard will occur in the absence of preventive controls.”1 Notably, the FDA has recognized that prerequisite programs, such as a biosecurity plan, can be considered during this probability assessment. Individuals conducting the probability assessment may also need to utilize resources such as those from FDA recalls or the Reportable Food Registry, as well as their own facility history, to make this determination. As in the assessment of severity, the probability of hazard occurrence is highly dependent upon the facility. For example, Salmonella contamination is a concern across animal feed in general, but its prevalence and severity in swine feed is lower than in many non-livestock species. This is demonstrated by the FDA Salmonella Compliance Policy Guide,16 which describes that pet food is considered adulterated when it is contaminated with Salmonella and will not subsequently undergo a commercial heat step or other commercial process that will destroy the salmonellae. However, feed for other animals is considered to be adulterated only when it is contaminated with a Salmonella serotype that is considered to be pathogenic to the animal intended to consume the feed and the feed will not subsequently undergo a commercial heat step or other commercial process that will kill the salmonellae.16 The only pathogenic Salmonella serotype that has been associated with salmonellosis is Salmonella enterica serovar Choleraesuis, which is rarely found in the environment outside of the pig, and the probability for this serotype transmission through feed and ingredients is negligible.16 Still, Salmonella may be a hazard of importance for individual feed mills that manufacture feed for other species if their prohibited serotypes are more probable to occur or if the mill exports feed to countries with more stringent standards, such as those in many European countries. Depending upon the serotype, the facility design, its ingredients, and its customers, assessment of the severity of Salmonella and other hazards will likely differ among feed mills.
Once hazards are identified and their severity and predictability are established, it must be determined if their combination requires specific controls. Preventive controls according to FSMA require stringent management components, such as monitoring, validation, verification, corrective action, and a recall plan.1 While many of these control strategies are useful, most feed mills manufacturing solely swine feed will likely have no hazards with the combination of probability and severity that requires a preventive control. Instead, most facilities will likely choose to mitigate hazards by reducing their probability with prerequisite programs, such as a biosecurity program. The following strategies describe these potential biosecurity program components that may be used to reduce the probability of biological hazards such as PEDV in swine feed.
Hazard mitigation
Prevention of hazard entry during ingredient receiving
One of the most effective components of feed mill biosecurity is prevention of hazard entry during the receiving of ingredients.3 There is incentive to prevent a hazard’s entry into a facility altogether, because the European Food Safety Authority (EFSA) has shown that the introduction of a contaminated material into a feed mill can lead to the mill being contaminated for an extended period.17 The first step for hazard prevention during receiving is to develop a supplier program that includes purchase specifications clearly communicating your expectations for the safety of inbound ingredients. This may also include verification of ingredient-supplier protocols and on-site manufacturing facility reviews and assessments. Once those specifications are in place, it is important to communicate and enforce them. It should be noted that methods employed on hazards evaluated to not require a preventive control can be mitigated through a biosecurity plan. However, these same activities used to control a hazard that requires a preventive control would require a supply-chain program as a supply-chain-applied control, which requires a number of management components and documentation under FSMA.1
Regardless of the hazard evaluation determination, prevention of a biological hazard typically includes a sampling and analytical schedule for its presence in high-risk ingredients. Sampling protocols should be constructed to identify sampling method, quantity needed to collect, sample labeling, retention procedures, and directions for analysis.3 The Association of American Feed Control Officials’ “Good Samples: Guidance” on obtaining defensible samples outlines aseptic sampling methods to obtain a high-quality representative sample from various types of ingredients.18,19 Aseptic sampling is required for biological pathogens, because there is a high potential for cross-contamination of samples during the collection process. The schedule should also include testing and holding procedures, as well as instructions for appropriate analysis. The sampling and analytical schedule will again be dependent upon each feed mill’s assessment of hazards, its potential risk in ingredients, and its available analytic capabilities. If an ingredient is considered high risk, every lot should be analyzed separately. If it is lower risk, it may be more practical to collect samples and pool them for more intermittent analysis.
The receiving process is also an area where emphasis can be placed on requirements for inbound trucks. Instructions for appropriate security measures for truck drivers and visitors should also be posted on proper signage (Figure 2).3 Ideally, drivers should stay inside their trucks at all times to minimize foot traffic. If the driver must exit the vehicle, he or she should wear disposable plastic boots or cover-ups to limit their potential for introducing hazards from their shoes.20 Recommendations for feed mills producing feed for high-risk facilities, such as those supplying breeding-stock multipliers, have been established by PIC North America.20 Their suggestions to maintain biosecurity are applicable to many swine feed mills trying to mitigate biological hazards through a biosecurity plan. All trucks entering the feed mill should have mud and sludge removed from the trailer opening before the vehicle reaches the pit, and the pit should remain covered until the truck is ready to unload (Figure 3).20 Appropriate documentation, such as receiving records that include the date, time, and lot number during unloading, should also be gathered in order to allow traceability of feed and ingredients. Documentation from inbound trucks regarding previous loads should also be collected. Regardless, if ingredients enter the feed mill in bagged, bulk, or liquid form, particular emphasis should be placed on sampling and hazard analysis of high-risk ingredients prior to unloading. This is particularly true for bulk ingredients that typically enter through a central pit and travel through bucket elevators, turn heads, and conveyors to storage bins. Ingredients may be contaminated prior to unloading, but they may also be contaminated during the unloading process due to mud or floor sweepings intermingling with ingredients in the pit. Cones and funneling devices (Figure 4) can also be used to limit the quantity of material that spills during unloading and prevent people from sweeping spilled ingredients into the pit.20 Floor sweepings, including those from the unloading process, should be disposed of and not swept into the pit. Historically, there has been little emphasis on the unloading and sequencing of high-risk ingredients or the disposal of floor sweepings in other locations, but these practices should be considered to reduce the risk of undesirable microorganism contamination in inbound ingredients.17 This is particularly true because it is not practical to clean the receiving pit and the conveying equipment on a frequent basis, and they may have ingredient residue that can lead to ingredient-to-ingredient cross-contamination (figures 5 to 7).
Figure 2: Example biosecurity sign with directions for truck drivers

Figure 3: Example of potential contamination entering the dump pit by truck

Figure 4: Funneling cone to limit spills at the receiving pit

Bagged ingredients are typically stored in their original bags within the warehouse until used, while liquids are unloaded into a storage tank that may or may not be heated. Segregation of bagged ingredients into heated storage areas with holding times have been implemented in some production systems to reduce the risk of hazard probability. For example, some feed mills hold high-risk ingredients for 2 weeks at room temperature prior to use to decrease their risk of containing PEDV.21 Bagged ingredients should also be checked to ensure that bags are intact and dry. Lot numbers should be recorded and bins should be emptied and documented when changing lots to improve traceability. Finally, liquid ingredient valves should be locked when not in use to reduce the risk of incorrect addition into a specific tank. If the ingredient is heated, steps should be taken to prevent microbial growth in the water fraction of the liquid as necessary.
Prevention of hazard entry due to people
One of the most overlooked areas and greatest risk of hazard entry is people. Those working in the feed mill and visitors such as guests, truck drivers, and subcontractors have the ability to introduce contaminants into a system. Some of the most common breaches in biosecurity occur when visitors such as subcontractors enter the facility. People may unknowingly carry fecal, dirt, or dust particles contaminated with undesirable microorganisms on the bottoms of their shoes or on clothing, and are at a particularly higher risk if they are coming from another farm or feed mill where the hazard is present.22 People movement considerations for biosecurity on swine farms were refined to reduce the transmission of porcine reproduction and respiratory syndrome (PRRS) virus, but those procedures were not often extended to the feed mill because it was not a high risk factor for PRRS virus transmission.22,23 However, the research associated with that virus demonstrates how biosecurity programs help reduce transmission from viral particles on shoes, clothing, and the human body. 22,23 The concept of biosecurity protocols to reduce the risk of biological hazard transmission by restricting personnel movement is relevant to apply to the feed production system now that PEDV has been shown to be potentially transmitted through feed. These protocols can help reduce the risk of hazard introduction by truck drivers and other non-mill employees, as previously discussed, or by reducing the likelihood that a feed mill employee will track a potential hazard throughout the mill. To better understand the magnitude of the potential risks of foot traffic, recent research with PEDV can be used as an example. No-walk zones or even hygienic zoning may be appropriate to include in biosecurity plans in feed mills that have a high probability of having PEDV because such a low concentration of the virus can result in widespread disease. On the basis of the known minimum infectious dose of PEDV, 1 gram of contaminated pig feces has enough viral particles to result in 500 tons of potentially infectious feed.24 Thus, it is imperative to reduce the probability of even a seemingly insignificant amount of feces, particularly at open locations such as receiving-pit grates or hand-add ports. Controlling foot traffic across these grates is a logical, low-cost method to reduce pathogen transmission risk.
When considering the control of individuals, it is also recommended that log books be available to document the entry and exit times of visitors.3 Procedures should outline that visitors must be accompanied at all times by a trained employee to help prevent biosecurity breaches. Visitors should be provided clean footwear, plastic boots, or boot cover-ups to limit the entry of outside hazards.3 Finally, signage should be displayed in appropriate areas to communicate off-limit areas.3
Prevention of cross-contamination hazards during production
Along with their direct presence in the feed, a concern with biological hazards is potential for long-term cross-contamination in the feed mill. In one study,14 8.8% of ingredients of animal origin collected from three feed mills were found to be contaminated with Salmonella, but dust samples had a contamination rate of 18.5%. If biosecurity measures fail and undesirable microorganisms enter the facility, it is very difficult to remove those hazards from the system.14 Any location where there is the propensity for residual organic matter to remain within equipment after processing can lead to cross-contamination of subsequent batches or runs. Due to their designs, the highest risk for this to occur may be inside screw conveyers (Figure 5), inside coolers and storage bins (Figure 6), and in the boot pits of bucket elevators (Figure 7).
Figure 5: Screw conveyor with potential contamination
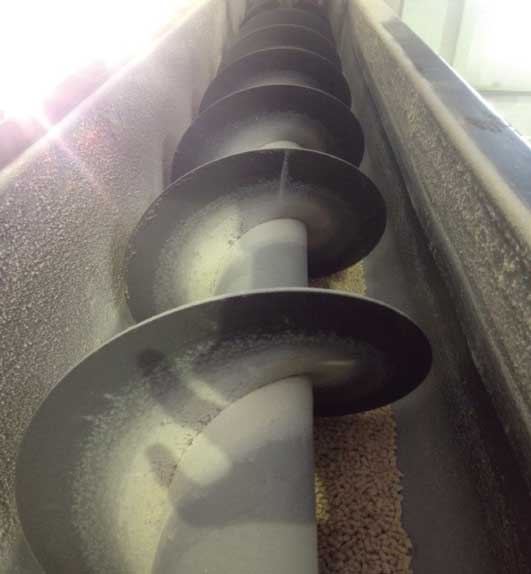
Figure 6: Surge bin with potential contamination

Figure 7: Bucket elevator with potential contamination

This type of carryover cross-contamination can be minimized by employing flushing and sequencing schedules as part of a biosecurity plan. By definition, flushing is “the process of running an ingredient, usually an abrasive-type material such as corn, soybean meal, peanut hulls, etc, through the manufacturing equipment and associated handling equipment after the production of a batch of feed, for the purpose of cleaning out any drug residue.”25 Alternatively, sequencing is “the preplanned order of production, storage, and distribution of different animal feeds designed to direct drug carryover into subsequent feeds which will not result in unsafe contamination.”26 Flushing and sequencing protocols have been used for years to reduce the risk of batch-to-batch drug carryover, and the same concepts can be applied to mitigate biological hazards. The flushing or sequencing protocol should consider all parts of the manufacturing process, from receiving through load-out. In specific high-risk instances, both flushing and sequencing, or multiple sequences, may be required. Preliminary data from our laboratory indicates that infective PEDV is still present in the second feed batch sequenced after the manufacturing of a contaminated batch (unpublished data). Thus, sequencing should be considered a risk-reduction procedure but not a risk-elimination procedure.
In addition to sequencing and flushing, the maintenance of a housekeeping schedule can also help prevent cross-contamination of biological hazards.3,20 This schedule can include sweeping production areas such as the floors and hand-add areas on a regular basis and disposal of the sweepings into the trash, not into the next batch of feed. Particular emphasis on housekeeping should occur in high-traffic areas and locations with entry into feed-contact surfaces. An important part of housekeeping is dust collection. Notably, many feed mills place dust from the air-collection systems and floor sweepings directly back into the feed system to limit shrink. However, this dust should be considered high risk and discarded.17 Recent data27 evaluating the environmental contamination when manufacturing PEDV-infected feed suggests that potentially infective dust particles can be widely dispersed throughout the feed manufacturing area.
Prevention of cross-contamination hazards during load-out and delivery
Reducing the risk of hazard introduction by potential cross-contamination from outbound trucks is important to ensure feed safety. The exterior, top, and interior compartments of trucks may contain residual feed or ingredients that, if infectious, may lead to contamination of newly manufactured feed during the loading and delivery process (Figure 8). It is suggested that documentation is maintained to improve traceability, including the previous load hauled, shipment lot number and location, and time of loading.3 Feed-truck delivery should be coordinated so that feed is delivered to lower-risk farms prior to higher-risk farms, particularly if a single load must visit multiple locations.17 Some facilities have effectively incorporated truck washes, thermo-assisted decontamination drying, and sanitation methods for feed trucks to minimize the risk of contamination of the feed mill, feed, and farms.20
Figure 8: Potential contamination from leftover material in the top of a bulk feed truck

A biosecurity plan should also include specific directions for driver behavior during delivery. A contaminated environment around feed bins on farms can potentially result in the feed-truck driver transferring this contaminant to another location or back to the feed mill. Drivers should ideally stay in their vehicles during delivery, and an on-site worker should open bin lids.17 This is still relatively impractical for most sites, so drivers exiting vehicles should wear clean shoe covers or boots when exiting the vehicle and remove the shoe covers and sanitize their hands prior to re-entering their truck.3,20 Drivers that exit feed trucks should never directly enter barns or have direct contact with pigs or fecal material. Particular attention should be paid to avoiding areas around exhaust fans, dead-stock disposal areas, and livestock-contact areas where the driver may come in contact with infective fecal or other material, such as load-out chutes. Protocols for reporting and addressing feed spills should be in place.
Drivers should be aware that survival of most biological hazards is greatest during cold conditions, so winter may require enhanced protocols. In addition, manure disposal periods may create particularly challenging times for preventing cross-contamination during feed delivery. Large volumes of infectious fecal material may be present, and cross-traffic with manure-application equipment may be unavoidable, again requiring enhanced sanitation protocols.
Finally, it is critical that farm personnel communicate herd-health status to feed-mill personnel. Pathogen shedding is greatest during the early stages of infections. This increased load of undesirable microorganisms can lead to elevated contamination of the environment around the farm, which may include the areas around feed bins. Knowing the status of a site is important for assessing risk and scheduling of deliveries to reduce risk of inadvertently contaminating other sites through subsequent deliveries. Another responsibility of farm personnel is to communicate to feed-mill staff the potential consequences of risk of infection to the site. On sites that are particularly sensitive due a high economic cost of infection or potential downstream implications, eg, boar studs or multiplier farms, protocols may be justified that might not be practical on many commercial sites.
Proactive reduction of biological hazards
Beyond prevention of entry and cross-contamination, proactive activities help reduce the risk of undesirable microorganisms. For example, thermal processing by pelleting has been demonstrated to mitigate the quantity of PEDV and Salmonella.24,28 While pelleting does not result in complete eradication of most bacterial pathogens, it serves to significantly reduce most biological hazards. However, it must be recognized that pelleting is a point-in-time mitigation step that does not prevent subsequent recontamination during the manufacturing or delivery process.24,28 For example, immediately after exiting the pellet mill, pellets are typically discharged into a cooler where the air used to bring pellets to ambient temperature has been drawn from inside the mill.
An option to reduce the likelihood of this cross-contamination after pelleting or in mash feeds or ingredients is to include a chemical additive. The chemicals, such as formaldehyde and medium-chain fatty acids, often carry residual activity that may reduce or prevent post-processing cross-contamination.29,30 Formaldehyde is an approved feed additive to prevent contamination of animal feed with Salmonella, but proper application requires appropriate equipment and a high level of training to prevent worker health and environmental dangers. Other chemical additives, such as medium-chain fatty acids, appear to be more user-friendly and have efficacies similar to that of formaldehyde, but current tested concentrations are uneconomical and impractical for implementation.29,30 Further research is important to evaluate the value of more practical inclusion levels of these feed additives.
In summary, prevention of the biological hazard entry is the first priority of a biosecurity plan. However, an effective plan should also address methods to reduce cross-contamination or to proactively mitigate the hazard if it enters the facility. A holistic approach to feed mill biosecurity is necessary to maximize risk reduction of microbial hazards.
Assessments
The final step of a biosecurity plan should be an assessment to evaluate the effectiveness of the implementation plan and expose areas of risk that should be addressed.3,20 It is helpful to design a self-assessment with simple “Yes” and “No” answers and space for further documentation. An example form is available at http://picgenus.com/health.aspx (click on Feed Mill Assessment Form). We have found that a preprinted form is useful in the field when performing assessments to ensure all areas of concern are covered and to provide a framework for developing ongoing improvement in protocols. The written assessment can be used as a basis for modifying behaviors to improve animal feed safety. Proactive assessments are most useful if conducted at 3- to 12-month intervals or prior to high-risk transmission seasons.20 The assessor should first assess effectiveness of biosecurity plans, but also should identify opportunities for improvement of the efficacy and feasibility of these plans. This assessment may be performed by an employee directly from the mill, from someone in the company that is employed outside the mill, or by a third party. In addition to assessments for biosecurity, several other certification programs, such as Safe Feed/Safe Food and Hazard Analysis Critical Control Point (HACCP), that include concepts of a biosecurity plan, may help reduce the probability of biological hazards.
Conclusions and future approaches
The emphasis on feed mill biosecurity has increased due to research demonstrating that feed can be a potential vector for biological hazards such as PEDV. A biosecurity plan requires identification and evaluation of hazards, as well as methods to reduce the probability of occurrence of biological hazards that are known or reasonably foreseeable. A summary of suggested practices and key points is provided in Box 1, and an example assessment form is available at http://picgenus.com/health.aspx (click on the Feed Mill Assessment Form). An assessment strategy may help facilities to evaluate effectiveness and identify gaps in their biosecurity plans. Future research is needed to continue to quantify the relative risk of pathogens in various feeds and ingredients to particular species, and to elucidate improved mitigation methods. Still, employing a biosecurity plan is a key method to extend biosecurity concepts from the farm to the feed mill, which may reduce the probability of biological hazards in feed and therefore improve herd health, economic security, and farm-to-fork food safety. It is important to note that implementation of these biosecurity measures will have certain costs associated with them, but strategic implementation of even some recommendations will reduce the level of risk.
Box 1: Summary of suggested practices and key points for assessment of feed-mill biosecurity
- Complete a hazard identification and evaluation process to understand key hazards that require mitigation within a feed mill.
- Dump pits, screw conveyors, and bucket elevators are difficult to clean once contaminated: preventing entry of contaminated ingredients into the mill should be a high priority.
- Develop purchase specifications with safety expectations of inbound ingredients and communicate those expectations to trusted suppliers.
- Create ingredient and finished-feed delivery expectations, such as truck sanitation and delivery sequencing procedures, and specify required documentation, such as previous load tracking and confirmation of truck cleanliness.
- Covers should remain over the dump pit until the truck is ready to unload, and care should be taken to prevent material (eg, sweepings) from entering the dump pit.
- Use flushing and sequencing to reduce the probability of batch-to-batch cross-contamination.
- Reduce the likelihood of cross-contamination by people.
- Post signage to communicate zoning expectations for truck drivers and guests.
- Providing clean footwear, plastic boots, or covers within feed mills or during delivery can reduce pathogen transfer.
- Require farms to report sites with clinical disease outbreaks and appropriately sequence truck delivery to reduce the risk of biological-hazard transfer back to the feed mill.
- Do not accept rejected feed previously in a bin on a farm.
- If possible, require drivers to remain inside trucks during feed loading and delivery, or at least utilize segregated boots or boot covers and hand sanitation.
- Prohibit feed-truck drivers from entering barns and request their avoidance of exhaust fans, dead-stock disposal, or cross-traffic with manure disposal equipment.
- Reduce the probability of environmental cross-contamination.
- Develop housekeeping schedules that require regular cleaning of equipment and sweeping floors.
- Dust is capable of carrying high numbers of undesirable microorganisms; collected dust should not be placed into the manufacturing system.
- Proactively mitigate biological hazards when appropriate.
- Thermal processing significantly minimizes the presence of many biological hazards, but is a point-in-time mitigation step that does not prevent post-processing cross-contamination.
- Chemical treatment of ingredients or feeds may provide residual ability to prevent cross-contamination, but many current chemical-additive options require specific equipment or specialized permits, or may not be economically feasible.
- An assessment helps determine effectiveness of a biosecurity plan and identifies gaps.
- A self-audit should be conducted every 3 to 12 months, depending upon the risks of the feed mill.
- Second- and third-party audits and certification programs are helpful to more aggressively evaluate the biosecurity plan.
It is important to point out that this review was written using a systematic approach to describe key concepts used in developing specific swine feed mill biosecurity plans. The listed recommendations should not be viewed as requirements unless noted. It is also important to understand that implementation of some of these recommendations may result in added costs to the feed mill and require additional employees and training. Not all these recommendations are appropriate for all facilities, but utilization of a biosecurity plan is a valuable tool to help improve animal feed safety.
Conflict of interest
Dr Fahrenholz certifies that his affiliation with or financial involvement with the subject matter of materials discussed in the manuscript is disclosed and described fully as follows: assistant professor, North Carolina State University, extension acitivities related to feed milling; and private consultant to the feed-milling industry.
Disclaimer
Scientific manuscripts published in the Journal of Swine Health and Production are peer reviewed. However, information on medications, feed, and management techniques may be specific to the research or commercial situation presented in the manuscript. It is the responsibility of the reader to use information responsibly and in accordance with the rules and regulations governing research or the practice of veterinary medicine in their country or region.
References
1. Federal Register. Current Good manufacturing practice, hazard analysis, and risk-based preventative controls for food for animals. 21 CFR. Part 507. 2015. Available at https://www.federal register.gov/arti/2015/09/17/2015-21921/current-good-manufacturing-practice-hazard-analysis-and-risk-based-preventive- controls-for-food-for. Accessed 18 February 2016.
2. Levis D, Baker R. Biosecurity of pigs and farm security. University of Nebraska-Lincoln Extension Website. 2011. Available at extension publications.unl.edu/assets/pdf/ec289.pdf. Accessed 12 February 2016.
3. American Feed Industry Association. Developing biosecurity practices for feed and ingredient manufacturing. Available at http://www.afia.org/rc_files/645/guidance_for_developing _biosecurity_practices_2015.pdf. Accessed 11 February 2016.
4. Reportable food registry. 21 U.S. Code § 350d 2011. Available at https://www.gpo.gov/fdsys/pkg/USCODE-2010-title21/pdf/USCODE-2010-title21-chap9-subchapIV-sec350f.pdf. Accessed 18 February 2016.
5. Saif LJ, Pensaert MB, Sestak K, Yeo S, Jung K. Coronaviruses. In: Zimmerman JJ, Karriker LA, Ramirez A, Schwartz KJ, Stevenson GW, eds. Diseases of Swine. 10th ed. Ames, Iowa: Wiley and Sons; 2012:501–524.
6. Pujols J, Segalés J. Survivability of porcine epidemic diarrhea virus (PEDV) in bovine plasma submitted to spray drying processing and held at different time by temperature storage conditions. Vet Microbiol. 2014;174:427–432.
7. Chen Q, Ganwu L, Stasko J, Thomas J, Stensland W, Pillatzki A, Gauger P, Schwartz K, Madson D, Yoon K, Stevenson G, Burrough E, Harmon K, Main R, Zhang J. Isolation and characterization of porcine epidemic diarrhea viruses associated with the 2013 disease outbreak among swine in the United States. J Clin Microbiol. 2014;52:234–243.
8. Dee S, Clement T, Schelkopf A, Nerem J, Knudsen D, Christopher-Hennings J, Nelson E. An evaluation of contaminated complete feed as a vehicle for porcine epidemic diarrhea virus infection of naïve pigs following consumption via natural feeding behavior: proof of concept. BMC Vet Res. 2014;10:176. doi:10.1186/s12917-04-0176-9.
9. Pasick J, Berhane Y, Ojkic D, Maxie G, Embury‐Hyatt C, Swekla K, Alexandersen S. Investigation into the role of potentially contaminated feed as a source of the first‐detected outbreaks of porcine epidemic diarrhea in Canada. Trans Emerg Dis. 2014;61:397–410.
*10. Misener M. PEDV infected spray dried porcine plasma proteins, the Canadian experience. Proc Allen D. Leman Swine Conf, Carlos Pijoan Swine Disease Eradication Symposium: Feed biosecurity in the wake of PED. St Paul, Minnesota. 2014.
11. Lowe J, Gauger P, Harmon K, Zhang J, Connor J, Yeske P, Loula T, Levis I, Dufresne L, Main R. Role of transportation in spread of porcine epidemic diarrhea virus infection, United States. Emerg Infect Dis. 2014;872–874.
12. Alonso C, Goede D, Morrison R, Davies P, Rovira A, Marthaler D, Torremorell M. Evidence of infectivity of airborne porcine epidemic diarrhea virus and detection of airborne viral RNA at long distances from infected herds. Vet Res. 2014;45:73. doi:10.1186/s13567-014-0073-z.
13. Narayanappa A, Sooryanarain H, Deventhiran J, Cao D, Ammayappan Venkatachalam B, Kambiranada D, LeRoith T, Heffron C, Lindstrom N, Hall K, Jobst P, Sexton C, Meng X, Elankumaran S. A novel pathogenic mammalian orthoreovirus from diarrheic pigs and swine blood meal in the United States. mBio. 2015;6(3):e00593–15.
14. Li X, Bethune L, Jia Y, Lovell R, Proescholdt T, Benz A, Schell T, Kaplan G, McChesney D. Surveillance of Salmonella prevalence in animal feeds and characterization of the Salmonella isolates by serotyping and antimicrobial susceptibility. Foodborne Pathog Dis. 2012;9:692–698.
15. United States Department of Health and Human Services/United States Food and Drug Administration. Draft list of potentially hazardous contaminants in animal feed and feed ingredients. Rockville, Maryland. 2006. Available at http://www.fda.gov/downloads/animalveterinary/safetyhealth/animalfeedsafetysystemafss/ucm053715.pdf. Accessed 27 March 2016.
16. Food and Drug Administration. Compliance Policy Guide Section 690.800 Salmonella in Food for Animals. Available at http://www.fda.gov/downloads/ICECI/ComplianceManuals/ CompliancePolicyGuidanceManual/UCM361105.pdf. Published July 12, 2013. Accessed 12 February 2016.
17. European Food Safety Authority. Scientific opinion of the panel on biological hazards on a request from the health and consumer protection, directorate general, European commission on microbiological risk assessment in feeding stuffs for food producing animals. EFSA J. 2008;720:1–84.
18. Association of American Feed Control Officials. Good Samples: Guidance on obtaining defensible samples. Champaign, Illinois: Association of American Control Officials Inspection and Sampling Committee. 2015. Available at http://www.aafco.org/Portals/0/SiteContent/Publications/GOODSamples.pdf. Accessed 22 March 2016.
19. Kansas State University. Aseptic feed sampling technique. Webinar Series on Feed Biosecurity. October 2014. Available at https://www.youtube.com/watch?v=dX6BLn9WKGE&feature=youtu.be. Accessed 12 February 2016.
20. PIC North America. Feed biosecurity guidelines: practical standards for mitigating the risk of swine enteric coronavirus transmission via feed. 2014. Available at http://www.pic.com/Images/Users/1/BIOSECURITY/FeedBiosecurityGuidelinesPICmultiplicationSep302014(1).pdf. Accessed 12 February 2016.
*21. Goyal S. Interventions to control PEDV (porcine epidemic diarrhea virus) in feed and feed ingredients. National Pork Board. Available at http://www.pork.org/wp-content/uploads/2014/05/goyal-14-157-main4.pdf. Published May 20, 2014. Last updated December 31, 2014. Accessed 15 February 2016.
22. Amass S, Stevenson G, Anderson C, Grote LA, Dowell C, Vyverberg DV, Kanitz C, Ragland D. Investigation of people as mechanical vectors for porcine reproductive and respiratory syndrome virus. Swine Health Prod. 2000;8:161–166.
23. Otake S, Dee S, Rossow K, Deen J, Joo H, Molitor T, Pijoan C. Transmission of porcine reproductive and respiratory syndrome virus by fomites (boots and coveralls). J Swine Health Prod. 2002;10:59–65.
*24. Jones C, Stark C, Dritz S, Rigdon A, Woodworth J. Recent research into feed processing and biosafety. Proc ADSA-ASAS Midwest Meeting. 2015.
25. Food and Drug Administration. Compliance Program Guidance Manual. 7371.004. Feed Manufacturing. 2015. Available at http://www.fda.gov/downloads/AnimalVeterinary/Guidance ComplianceEnforcement/ComplianceEnforcement/UCM113430.pdf. Accessed 15 February 2016.
26. Food and Drug Administration. Compliance Policy Guides Section 680.600. Sequencing as a means to prevent unsafe drug contamination in the production, storage, and distribution of feeds. 2015. Available at http://www.fda.gov/ICECI/ ComplianceManuals/CompliancePolicy GuidanceManual/ucm074700.htm. Accessed 15 February 2016.
*27. Schumacher LL, Cochrane RA, Evans CE, Kalivoda JR, Woodworth JC, Stark CR, Jones CK, Main RG, Zhang J, Dritz SS, Gauger PC. Evaluating the effect of manufacturing porcine epidemic diarrhea virus (PEDV)-contaminated feed on subsequent feed mill environmental surface contamination [abstract]. Kansas Agricultural Experiment Station Research Reports. 2015;1(7).
*28. Cochrane R, Stark C, Huss A, Aldrich G, Knueven C, Pitts J, Jones C. Salmonella surrogate mitigation in poultry feed using a dry acid powder. Proc ADSA-ASAS Midwest Meeting. 2015.
*29. Cochrane RA, Dritz SS, Woodworth JC, Zhang J, Huss AR, Stark CR, Hesse RA, Tokach MD, Bai JF, Jones CK. Evaluating chemical mitigation of PEDv in swine feed and ingredients. Proc ADSA-ASAS Midwest Meeting. 2015.
*30. Cochrane RA, Huss AR, Jones CK. 2015. Evaluating chemical mitigation of Salmonella in animal feed ingredients. Proc ADSA-ASAS Joint Annual Meeting. 2015.
* Non-refereed references.