Preweaning mortality continues to be a cause for concern in the US swine industry. Current preweaning mortality estimates1 from US commercial swine operations have been relatively stable at 17.5% between 2015 to 2017. At a 20% preweaning mortality level, it has been estimated to cost the US pork industry $650 to $800 million annually.2 The majority of these losses occur during the perinatal period (during farrowing and the first 3 days after birth) and can account for up to 50% of total preweaning mortality.3 Preweaning mortality has been described as multifactorial and include low birth weight, lack of sufficient energy stores, poor body temperature regulation, or strong competition between littermates for colostrum and milk.4,5
Within the farrowing environment, the sow and her piglets are at two very different life stages and have different requirements regarding their thermal, social, and physical production system environments. For example, ambient temperature requirements for the lactating sow range from 15°C to 26°C, but a higher temperature of 34°C is preferred by individual newborn piglets.6,7 At birth, piglets are poorly equipped to deal with the environment they experience outside of the sow. They are especially susceptible to cold stress at birth because they lack a coat of hair, have a large surface area to body weight ratio, lack suitable energy reserves, and have poor body thermostability.8,9 When the environmental temperature falls below 34°C the newborn piglet is subjected to cold stress and will begin to mobilize its glycogen reserves from the liver and skeletal muscles. The newborn piglet increases heat production by consuming nutrient dense colostrum produced by the sow during the first few hours of lactation.10 Under cold stress, the piglet undergoes reduced locomotive vigor resulting from weakness through starvation leading to decreased capabilities to avoid movements exhibited by the sow.11,12 During lactation, littermates huddle to increase their thermal insulation and conduction.13,14 In conventional indoor confinement systems, caretakers can provide piglets with supplemental heat sources (eg, lamps and mats) in an attempt to keep the piglets warm and away from their mother to reduce preweaning mortality.
Previous work by Stinn and Xin15 compared a heat mat to a heat lamp on piglet mortality, rate of gain, and electric power use. The authors concluded that there was no difference in rate of gain or mortality, but mats used 36% less power compared to heat lamps. In agreement with this study, MacDonald and colleagues16 found that heat mats can have a 50% cost savings without detrimentally affecting piglet weaning weight or average daily weight gain. Finally, Hrupka and colleagues17 reported that heat lamp location within a farrowing stall did not affect preweaning mortality but did conclude that fewer piglets were within 8 cm of the sow and more were located in the area of the heat source. However, technology advancements in heat mats and heat lamps have occurred since these previous studies were published. Additionally, there are no publications to the authors’ knowledge in the scientific literature that examines the combination of heat source, piglet behavior, and the economics of various sources used to provide supplemental heat to piglets during lactation. Therefore, the objectives of this work were to 1) evaluate piglet performance and preweaning mortality when piglets are supplied with two different heat source treatments, 2) evaluate sow lying behavior and piglet location behavior in regard to heat source and proximity to the sow, and 3) evaluate the energy efficiency of two different heat sources.
Materials and methods
The research protocol was approved by the Iowa State University Institutional Animal Care and Use Committee (IACUC-18-256). Sows were allotted a minimum of a 72-hour acclimation period prior to farrowing.
Animals, location, and housing
A total of 17 sow and litter units housed at the Iowa State University Allen E. Christian Swine Teaching Farm in farrowing stalls during 2 farrowing groups (October to November 2018 and November to December 2018) were used in this study. The farrowing stalls used in this study had interlocking plastic flooring and a creep area on both sides of the sow. The total stall area measured 2.0 × 1.7 m2. The center sow area measured 2.0 × 0.6 m2 with two creep areas measuring 2.0 × 0.55 m2 on either side. Solid flooring, 1.2 × 0.4 m2, on one side of the piglet creep area was where the heat source was provided. The stalls were distributed across 2 farrowing rooms (7 stalls per room) located in a negative-pressure, mechanically ventilated barn set at 21.1°C. Each stall contained a sow and her litter with no cross fostering, and the stall was the experimental unit. Multiparous crossbred sows (parity 1 = 5; 2 = 3; 3 = 4; 4 = 1; and ≥ 7 = 4) were randomly assigned to a treatment prior to entering the farrowing room. Sows were provided ad libitum access to water via one nipple and were hand fed once daily prior to farrowing. Post farrowing, sows were hand fed to appetite 3 times daily in 0.9 kg increments. All diets were prepared by a commercial feed mill (Key Cooperative) composed of primarily corn, soybean meal, dried distillers grains, and nutrients formulated according to NRC (2012) guidelines to meet or exceed gestating and lactating sow nutrient requirements. The diet contained 19.6% crude protein, 32 Mcal metabolizable energy/kg, and 1.17% total lysine.
Treatments
Two treatments were compared: Baby Pig Heat Mat - Single 48 (MAT; Kane Manufacturing; 85 W; 34.29 × 121.92 cm2; polyethylene; n = 8; Figure 1) and Poly Heat Lamp Fixture (LAMP; Hog Slat; n = 9; 125 W; 25.4 × 30.48 cm2; polypropylene; Figure 2). The heat lamp thermal zone used for piglet observation was an area covering 40 × 121 cm2.
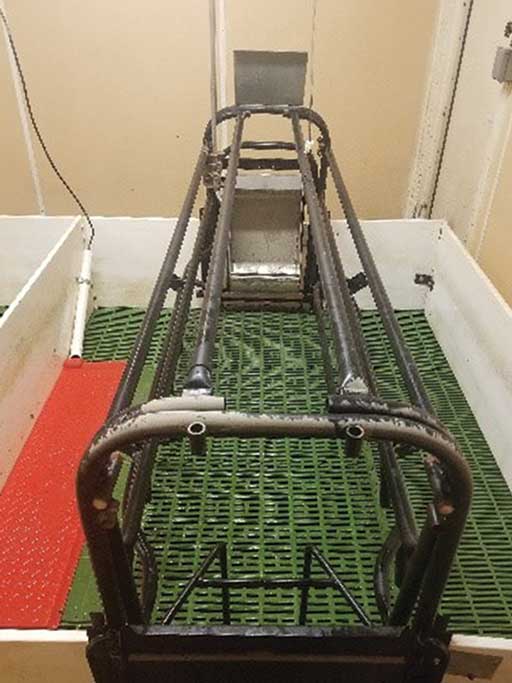
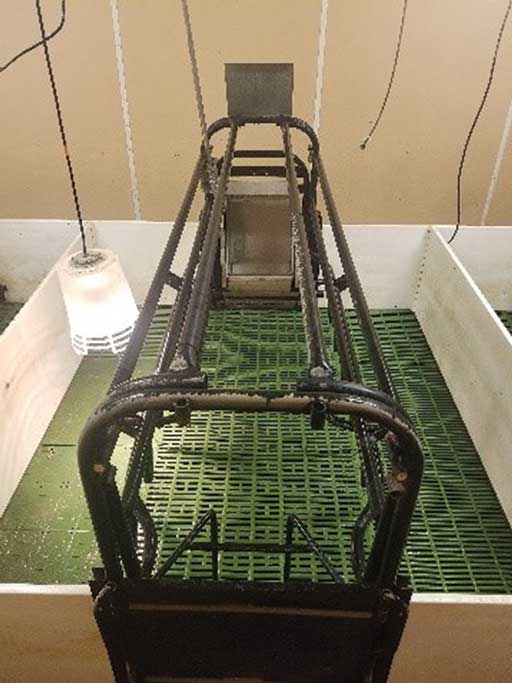
Both heat sources were set at 32.2°C. The LAMP was controlled via a single step mechanical thermostat for a maximum temperature and height was adjusted to match the temperature regimen of MAT, which was controlled via Thermostat Programmable 1 Zone (Kane Manufacturing). Heat source temperatures were confirmed with an infrared temperature gun (Tool House Digital Infrared Thermometer; model 770343S; Alltrade Tools, LLC; accuracy: 2°C). Sows and their piglets were blocked by parity and assigned to one of the heat source treatments throughout lactation. Mean piglet weaning age was 21 days.
Production measures
Piglets were counted and weighed at processing and weaning. Piglets were administered 1 mL of Iron Hydrogenated Dextran (VetOne) and 0.5 mL of Excede (Zoetis) following manufacturer and veterinary guidelines used when developing farm standard operating procedures. Number born alive was recorded for each litter. Preweaning mortality was defined as a loss incurred post farrowing and prior to weaning, calculated as percent mortality = (the number of pigs weaned/number of pigs born alive) × 100. Piglets were weighed individually on day 1 and at weaning using a digital scale (Mettler PM30-K; Mettler Toledo; accuracy: 0.5 g). All piglet deaths were recorded and included day, sex, and weight.
Behavioral evaluation
Sows and their litters were observed by a single trained observer at 2 time segments over a 24-hour period on days 1, 2, 3, 4, 5, week before weaning (DW), and day before weaning (DD) using a live observation methodology. Each time segment consisted of 2 consecutive hours (09:00 to 11:00 and 21:00 to 23:00) and observations were collected every 15 minutes. Observer training took place prior to the first farrowing until the undergraduate student observer had > 95% agreement with the graduate student who developed the ethogram according to the study objectives and trained the observer. An ethogram was created that included 5 mutually exclusive sow postures, 2 piglet locations, and piglet contact with the sow (Table 1).
Measure* | Definition |
---|---|
Definition | |
Mat | 75% or more of the piglet is touching the heat mat |
Lamp | 75% or more of the piglet is under the heat lamp |
Other | Anywhere in the stall not associated with the heat source |
Piglet contact with dam | |
Touch | Any part of the piglet is touching the sow |
Not | No part of the piglet is touching the sow |
Sow posture | |
Lateral lie left | Pig lying on left side |
Lateral lie right | Pig lying on right side |
Sternal lie | Pig lying on sternum |
Standing | All four feet on flooring |
Sitting | Hindquarter on floor, front feet on flooring |
Electrical use
Kill-A-Watt EZ Meter P4460 (P3 International Corporation; accuracy: 0.02%) were connected to the allotted heat source for the entire lactation duration to measure energy use by each experimental unit. Electric meter readings were monitored and recorded twice weekly by farm staff. Final energy use readings were recorded at weaning.
Statistical analysis
All data were evaluated using mixed model methodology (Proc Mixed; SAS version 9.4; SAS Institute Inc). Sources of model variation were considered significant at P < .05. When fixed effect model variation was significant, least squares means for each level within the fixed effect source were separated using the pdiff option within the Proc Mixed procedure. Fixed effects in the model included group, parity, location of heat source, and treatment. Production data were analyzed using a generalized mixed model (Proc Glimmix; SAS version 9.3; SAS Institute Inc). A random effect for the interaction between room and stall was included in the model. Behavioral data were analyzed using a generalized mixed model with i-link distribution (Proc Glimmix). Fixed effects in the model included day, treatment, and time. Random effects were room and stall.
Results
Production
No litter weaning weight (P = .85) or litter average daily gain (P = .79) differences were observed when comparing piglets provided heat lamps and piglets provided heat mats in the study (Table 2). No treatment differences were observed in preweaning mortality (P = .58). Sixty percent of mortalities occurred within the first 24 hours post farrowing.
Treatment | Litter wean weight†, kg | Litter average daily gain‡, kg/day | Mortality§, % |
---|---|---|---|
Lamp | 44.5 (8.50) | 1.5 (0.29) | 15.3 (2.52) |
Mat | 47.0 (8.86) | 1.6 (0.30) | 12.3 (3.32) |
* No differences in production traits observed (P ≥ .58).
† Piglets were weighed individually then summed together for litter weaning weight.
‡ Litter average daily gain = (litter wean weight – litter birth weight) / days of lactation.
§ Percent mortality = (total mortalities / total number born alive) × 100.
Behavior
The number of piglets using either a heat lamp or heat mat differed within a treatment day, with lamp being used by more piglets on day 1, 3, 4, DW, and DD (Figure 3; P < .001). The number of piglets using the heat lamp treatment across days of lactation decreased after day 4 (Figure 4; P < .001). Similarly, the number of piglets using the heat mat treatment over days of lactation decreased at DW until the end of lactation (Figure 5; P < .001).
The number of piglets in physical contact with their dam by treatment within lactation day differed, with MAT piglets having greater physical contact with their dam on day 3 and 4 (Figure 6; P < .001). The number of piglets in physical contact with their dam, within treatment, across days of lactation resulted in greater variation within LAMP treatment (Figure 7; P < .001). The number of piglets in physical contact with their dam, within treatment, over days of lactation demonstrated that the piglets’ physical contact with their dam remained relatively constant when provided supplemental heat using the MAT treatment (Figure 8; P < .001).
Sow lying behavior was not affected by heat source type or location (χ2 = 2.14, P = .14). As a result of sows spending most of the time lying laterally, analysis was focused on these traits. Sow lying preference demonstrated that 7 sows preferred to lay laterally right and 8 sows preferred to lay laterally left. Five sows favored lying with their udder toward the heat source and 10 favored lying with their udder away from the heat source. There were 2 sows that showed no preference for lying position and therefore udder direction to the heat source.
Energy
The mean (SD) energy consumption for the heat mat treatment (19.4 [2.99] kWh) was less than the energy use for the heat lamp treatment (68.5 [1.97] kWh) with a difference of 49.1 kWh/litter (P < .001). Initial heat lamp and heat mat costs vary, with heat lamps requiring less initial investment, but has a greater cost associated with energy use (Table 3). Using an average cost of $0.12/kWh in the Midwest,2 the average 49.05 kWh energy savings can be translated into an average energy cost savings of $5.89/litter (49.1 kWh × $0.12/kWh = $5.89).
Heat Mat† | Heat Lamp‡ | |
---|---|---|
Total farrowing house cost, $ | 27,520.00 | 4617.60 |
Cost/farrowing room, $ | 3440.00 | 577.20 |
Cost/farrowing stall | 86.00 | 14.43 |
Annual replacement cost, $ | 0.00§ | 1.58¶ |
Energy use/turn, kWh | 19.4 | 68.5 |
Energy use/y, kWh** | 291.3 | 1027.05 |
Energy cost/Year††, $ | 34.96 | 123.25 |
Total cost Year 1††, $ | 120.96 | 139.26 |
Payback period, mo | 11.7 |
* The example farm used in this analysis was an 8-room farrowing house that contains 4 rows/room and 10 stalls/row, with a total of 40 stalls/room and 320 total farrowing stalls in the farrowing house.
† Heat mat set up included Baby Pig Heat Mat – Single 48 (Kane Manufacturing) with controller and relays required to achieve energy savings. Costs for this setup provided by Kane Manufacturing.
‡ Heat lamp set up included one 125 W bulb per Poly Heat Lamp Fixture (Hogslat). Costs for this setup available at www.hogslat.com.
§ Heat mat replacement rate is every 7 to 10 years.
¶ Bulbs have a 5000-hour life or 208 days, therefore at least one replacement will be required per year.
** Assuming 15 turns/year (2 days prefarrowing, 21-day lactation, and 1 day for cleaning).
†† Assuming $0.12/kWh.
Discussion
Challenges continue to exist in the farrowing house for the caretaker to supply a suitable environment for the sow and her piglets immediately after parturition and through the lactation period.8 Consistent results across studies indicate that preweaning mortality will remain relatively constant regardless of supplemental heat source (ie, heat lamps or heat mats) used.15,17 The current study supports the production parameter findings from previous studies, with no supplemental heat source effects on weaning weight, daily gain, or preweaning mortality further indicating that heat source type should be a management decision regarding what works best within a particular system. In agreement with previous studies, the majority of preweaning mortality occurred within the first 24 hours post farrowing.18
During the first 24 hours, when mortality rates were the greatest, behavior findings showed a greater number of piglets spending time in contact with their dam across treatments. Other studies have reported that the day-old piglets spend 60% to 75% of their time nursing or lying near their dam regardless of supplemental heat source position.19 In the current study, heat source type did not affect this behavior. Several biological factors could provide an explanation for this piglet behavior difference. The sow provides nutrition for the piglet, which is critical for the piglet to produce heat so that it can maintain its thermodynamics. Additionally, milk let-down initially is constant, therefore piglet nursing bouts and teat fidelity have not been established until later in lactation. Other factors that may contribute to the piglets’ preference to lie next to or near the sow include odors and sounds the sow makes that might be comforting to piglets. However, further research is needed to identify factors truly associated with the piglets’ desire to lie next to or very near their dam. Regardless of motivation, the area around the sow remains dangerous to piglets with crushing being an imminent threat as the number one reason for piglet mortality continues to be crushing or laid on by the sow.12 After the initial 24 hours post farrowing, supplemental heat source use by piglets increased across treatments, likely as a result of better thermodynamics and nursing bouts being initiated. Sow posture was unaffected by supplemental heat source location, decreasing heat stress concern from the supplemental heat provided for piglets. Additional research work is needed to examine other supplemental heat source options and piglet preference or motivation for each heat source.
However, consideration should be placed on the energy savings when utilizing heat mats. Under the circumstances in the current study, energy savings can be achieved by controlling heat mats with a controller as compared to varying heat lamp height. Heat mats can result in a savings of $18.30/farrowing stall or a total of $5856 return on investment (ROI) in year 1, a 21.2% ROI (initial year savings = [initial cost of heat lamp + heat mat energy costs] – [initial cost of lamp + bulb replacement + heat lamps energy costs]). In subsequent years that do not require heat source replacement, a savings of $89.87/stall or $28,758.40 total ROI, or 104.5%, can be acquired (total savings with mat = energy cost of mat – energy cost of lamp). Given the energy savings of the heat mat, a payback period of 11.7 months can be achieved. As stewards of the land and the environment, according to the Pork Quality Assurance Plus Good Production Practices, additional value can be found in minimizing the carbon footprint of swine production.20
Implications
Under the conditions of this study:
- Choice of mats or lamps can be based on factors other than pig performance.
- Energy savings can be achieved by using heat mats with a controller.
Acknowledgments
This project was funded in part by Kane Manufacturing. Support from the Department of Animal Science, College of Agriculture and Life Sciences at Iowa State University, and the US Department of Agriculture. A special thanks to the farm staff at the Allen E. Christian Iowa State University Swine Teaching Farm for their assistance in completing this project.
Conflict of interest
None reported.
Disclaimer
Scientific manuscripts published in the Journal of Swine Health and Production are peer reviewed. However, information on medications, feed, and management techniques may be specific to the research or commercial situation presented in the manuscript. It is the responsibility of the reader to use information responsibly and in accordance with the rules and regulations governing research or the practice of veterinary medicine in their country or region.
References
*1. Stalder KJ. 2018 pork industry productivity analysis. https://www.pork.org/wp-content/uploads/2018/09/2018-pork-industry-productivity-analysis.pdf. Published September 11, 2018. Accessed June 3, 2019.
*2. Average energy prices for the United States, regions, census divisions, and selected metropolitan areas. US Bureau of Labor and Statistics. https://www.bls.gov/regions/midwest/data/averageenergyprices_selectedareas_table.htm. Accessed June 3, 2019.
3. Vaillancourt JP, Marsh WE, Dial GD. Perinatal mortality in 48 North American swine herds. Swine Health Prod. 1994;2:13-18.
4. Fraser D, Rushen J. Colostrum intake by newborn piglets. Can J Anim Sci. 1992;72:1-13.
5. Svendsen J. Perinatal mortality in pigs. Anim Reprod Sci. 1992;28:59-67.
*6. National Pork Board. Swine Care Handbook. Des Moines, IA: National Pork Board; 2018. http://www.porkcdn.com/sites/all/files/documents/PQAPlus/V4.0/Details_Ref_SPS/2018SwineCareHandbook.pdf. Accessed March 20, 2020.
7. Curtis SE. The physical environment and mortality. In: Varley MA, ed. The Neonatal Pig: Development and Survival. Wallingford, United Kingdom: CAB International; 1995:269-285.
8. Johnson AK, Marchant-Forde JN. Welfare of pigs in the farrowing environment. Iowa State University Digital Repository. 2009. Accessed June 3, 2019. https://lib.dr.iastate.edu/ans_pubs/103.
9. English PR, Morrison V. Causes and prevention of piglet mortality. Pig News Inf. 1984;5:369-375.
*10. Johnson AK. Behavior, physiology and performance of sows and their litters produced on a sustainable pork farm [PhD thesis]. Lubbock, Tx: Texas Tech University; 2001. https://ttu-ir.tdl.org/handle/2346/12522.
11. Arey DS, Petchey AM, Fowler VR. The effect of straw on farrowing site choice and nest building behaviour in sows. Anim Sci. 1992;54:129-133.
12. Aumaitre A, Le Dividich J. Improvement of piglet survival rate in relation to farrowing systems and conditions. Ann Rech Vet. 1984;15:173-179.
*13. Bel Isle DM, England DC. Association of some individual factors and high mortality litters with porcine neonatal death. Proc Western Section ASAS. East Lansing, Michigan. 1978;80-82.
14. Mount LE. Environmental temperature preferred by the young pig. Nature. 1963;199:1212-1213.
*15. Stinn JP, Xin H. Heat lamp vs heat mat as localized heat source in swine farrowing crate. Ames, IA: Iowa State University; 2014. Animal Industry Report: AS 660, ASL R2931.
*16. MacDonald R, Feldmann T, Wrigglesworth M. Comparison of heat lamp to heat pad creep heat in farrowing units. Swine Housing: Proc 1st Int Conf. Des Moines, IA. 2000:357-364.
17. Hrupka BJ, Leibbrandt VD, Crenshaw TD, Benevenga NJ. The effect of farrowing crate heat lamp location on sow and pig patterns of lying and pig survival. J Anim Sci. 1998;76(12):2995-3002.
18. Bille N, Nielsen NC, Larsen JL, Svendsen J. Preweaning mortality in pigs. 2. The perinatal period. Nord Vet Med. 1974;26:294-313.
*19. Le Dividich J, Herpin P, Rousseau P. How extreme environmental temperatures and nutrition affect the survival on the growth rate of piglets. Proc Teagasc Pig Farmers Conf. Fermoy, Kilkenny, and Longford, Ireland. 2006:1-12.
*20. National Pork Board. Environment. In: Pork Quality Assurance Plus Education Handbook. 4th ed. Des Moines, IA: National Pork Board. 2019:66-68. http://www.porkcdn.com/sites/all/files/documents/PQAPlus/V4.0/Forms/PQAv4e_Handbook.pdf. Accessed March 20, 2020.
* Non-referred references.